Poor feeding conditions can also be a factor. Any kind of irregularity in the feed – whether from segregated feed, a misaligned feeder, or blockages or packing in the chamber – can cause performance to drop by up to 30%. Uneven distribution of material in the chamber means that the Hydroset – the mechanism that exerts an upward force on the mantle – cannot maintain even pressure. Depending on the type of irregularity, poor feeding conditions can either cause fluctuations in pressure over time, or in different parts of the chamber. Any fluctuation in pressure means that the optimal force will not be delivered consistently so, of course, crusher performance declines.
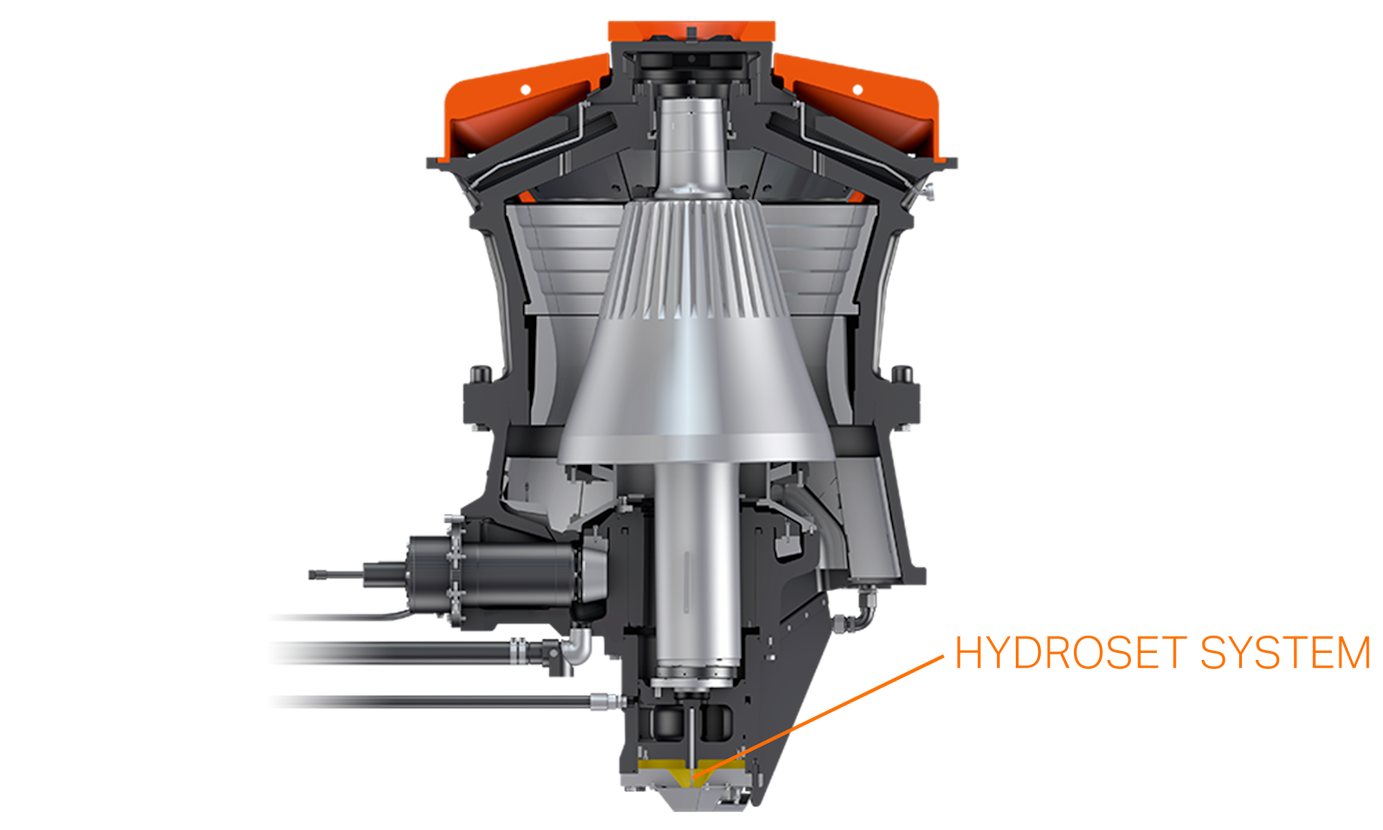
These are the two main causes of sub-optimal crushing performance, but losses in the reduction ratio can also be caused by selecting the wrong mantle or by having a poor chamber profile or design. Surprisingly, selecting the wrong alloy has no effect when it comes to the reduction ratio (although this will affect the life of wearable parts in your crusher). This graph summarizes the common problems affecting productivity:
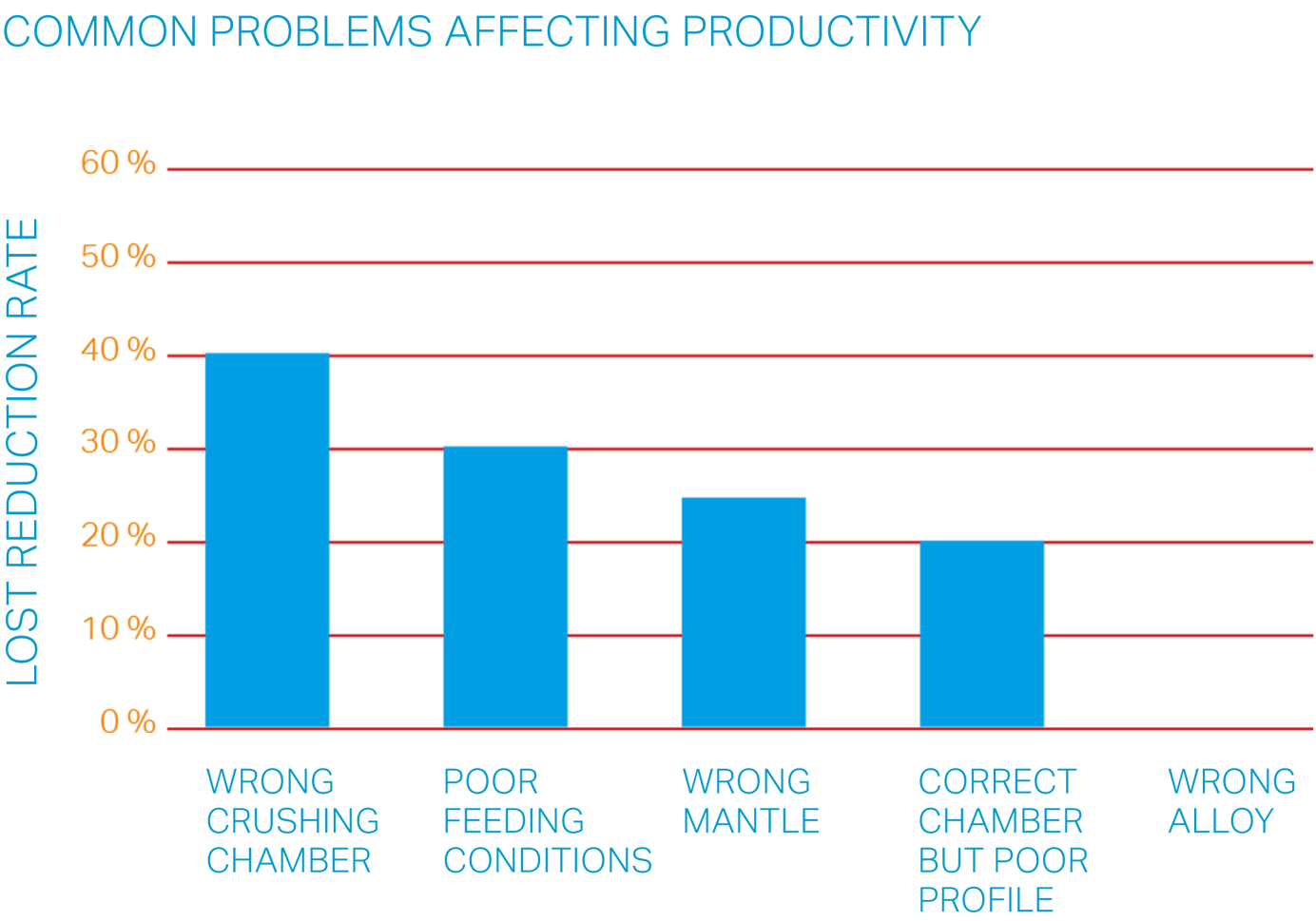